Nondestructive testing (NDT) dates back to the late-1800s, to the railroad industry. The “Oil and Whiting” method of crack detection was used to find damage in heavy steel parts. It was a simple yet effective test involving soaking the steel in oil, painting it white, allowing it to dry and then observing for brown marks that indicated a crack.
NDT has come a long way over the last 200 years. Using the very latest in science and technology it can now help towards ensuring the safety and efficiency of materials, components and systems, across multiple industries. Because it is a non-invasive technique, it is seen as the gold standard in evaluating new and in-situ items.
What is NDT?
Firstly, let’s define NDT or nondestructive evaluation (NDE) as it is sometimes called. It is a variety of methods by which an item is tested in such a way as to determine its compliance with a code or standard, or that it is still in a condition fit for its service. It can test new constructions and manufacturing and is also used to monitor the condition of materials or components that are in-service. Importantly, the main benefit of NDT is that the item can continue to be used once the testing is complete and it is deemed to have passed the inspection. In some cases, the item can be tested while in operation.
The ways in which NDT is used are diverse and compatible across a range of disciplines. Examples include: radiographing a weld to check that its imperfections are acceptable to the manufacturing standard; using ultrasound to measure the thickness of a ship’s hull plates; testing with an eddy current that a diver’s air cylinder has not suffered fatigue damage; and the use of a dye penetrant on an aluminum bicycle frame to ensure the joints are sound.
Who Can Perform NDT?
Now we have an idea of what NDT is and where it can be found, we should look at who can perform it. The answer is of course, a competent and qualified person. Competency is achieved by a combination of experience and appropriate instruction or training at a level certified as acceptable.
In general, the NDT industry has two common processes that define the qualifying requirements. One follows the International Standard of ISO 9712. This is a third-party scheme and once a technician has achieved the required experience and training, they are assessed by a body approved by the relevant nation’s regulatory authority. When the technician passes the theoretical and practical exams they become certified. Their employer then carries out job specific training, and upon successful completion of this they approve the technician to apply the NDT method(s) they have proved competent in. There are other schemes specific to industries, such as NAS 410 or EN 4179 in aerospace.
The other system follows the recommended practice SNT-TC-1a published by the American Society of Nondestructive Testing (ASNT). This is a second party scheme where the employer directly trains and examines the technician who works for them and thereby approves their competency to apply the method(s), as appropriate. Of course, the employer has to be competent to do this, so a Level III NDT professional will take care of the technical requirements. This person could be an employee or an appointed external body, specializing in this process.
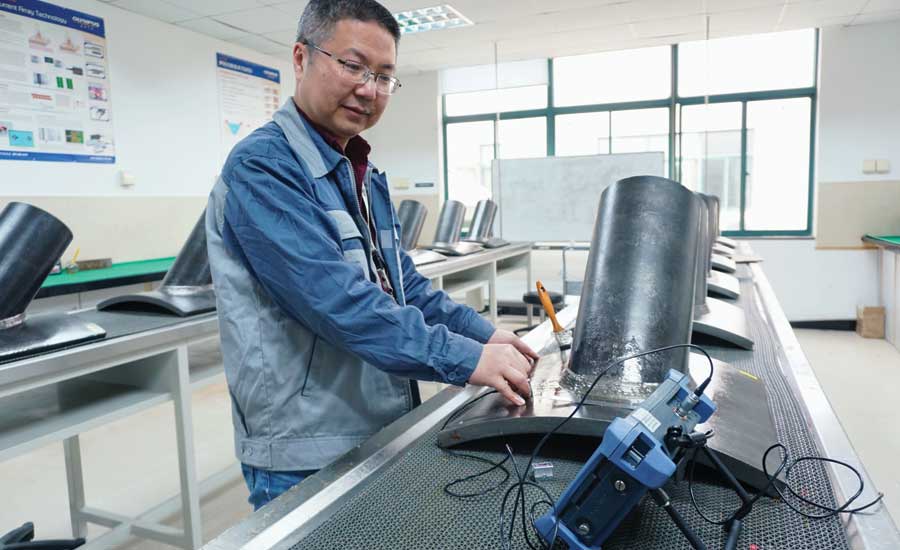
Competency is achieved by a combination of experience and appropriate instruction or training at a level certified as acceptable.
Qualification Standards
At this point, it is appropriate to explain the levels of NDT qualification. These are common for both of the qualification systems, ISO 9712 and SNT-TC-1a.
Firstly, a ‘trainee’ is a person who gains a level of basic experience needed for their industry. They learn specific working practices for their sector and the unique vocabulary that is required to fully understand the industry’s intricacies, such as technical terms, acronyms and slang.
The next stage is Level I and these technicians will have completed a minimum amount of time on On-The-Job Training (OJT), a specific number of classroom training hours, and passed the Level I exam, which includes an eyesight evaluation and continuous employment requirements. As a Level I technician they will be able to carry out NDT calibrations, testing and assess results against a written pass/fail criteria. These technicians must be operating under the direct control of a Level II or a Level III.
The Level II technician, having completed further OJT, classroom hours and qualifying exams, can carry out the duties of a Level I, as well as supervise Level I technicians. The Level II will also be able to evaluate the indications found by NDT either for identification or consideration against a code or standard to decide whether they are acceptable or not. Level II technicians may also develop test techniques based upon the requirements of an NDT procedure.
A Level III technician will have completed additional OJT, classroom hours and passed a higher-level examination. There are slight differences between the ASNT and the ISO 9712 Level IIIs. Both supervise lower level staff, and both develop and approve NDT procedures, but the ASNT Level III will also be able to train and qualify NDT staff under the SNT-TC-1a based schemes.
The ‘experience’ element of both systems is generally the same, that being that OJT is controlled and delivered by the employer. The classroom training requirement is generally aligned between the two systems as well, where a number of hours are allotted to each method. The ASNT system recommends a certain practice so it can be adapted by the employer to suit their needs, while ISO 9712 is more specific, with clearly defined and limited parameters.
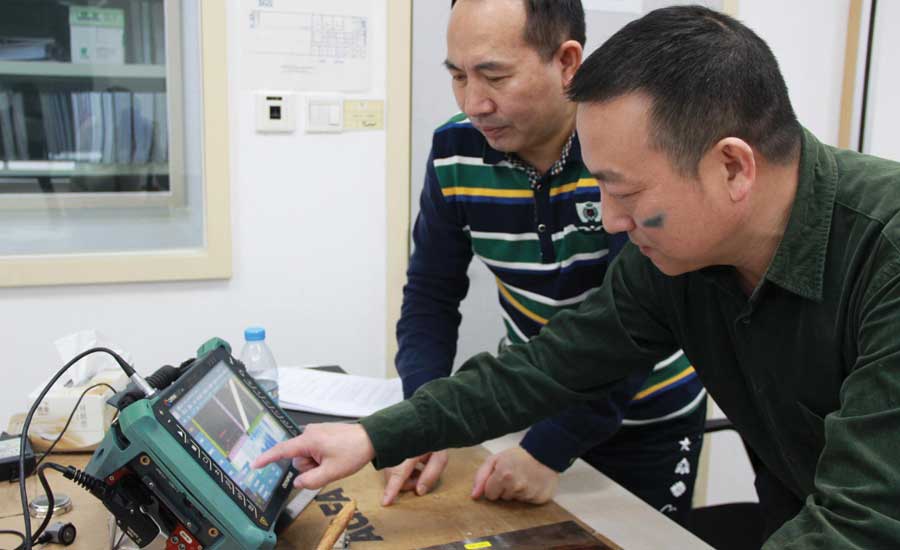
NDT is set to become even more important in the future as the emphasis on safety continues across all industries.
Proven Quality
The quality of the training in NDT is critical in the development of competent technicians. There is huge value in receiving training from a well-equipped, dedicated NDT training facility or company. Those with this expertise can offer a range of equipment and defective samples on which to learn and practice and have tutors with the experience and training themselves to deliver the course material, and importantly with expertise in their discipline.
Some ISO 9712 schemes, such as the one run by the British Institute of Non-destructive Testing (BINDT), called Personal Certification in Non-Destructive Testing (PCN), actually defines, audits and accredits training organizations that can deliver the training required (Approved Training Organizations, or ATO). Some of these are also accredited to deliver the certification examinations, namely an Authorized Qualifying Body (AQB).
The reliability of this system was proven recently when an ATO/AQB was found to be falsifying documentation. The ATO/AQB in question was immediately suspended and upon review removed from providing training and examinations in the future. In addition, all the staff had PCN certifications removed and were banned from working at another PCN ATO/AQB. As the integrity of the examinations were then in doubt, all technicians who had qualified through that organization were given the chance for a re-sit exam through another body of their choice.
Exciting Times Ahead
In conclusion, it is recommended to find a training center that has the experience and expertise that abides by either the SNT-TC-1a or ISO 9712 standards. The training course and final examinations should be accredited by an internationally recognized organization and delivered by or under the control of an appropriately trained and qualified Level III. It is important that the facility has a breadth of learning opportunities so that students can gain in-depth practice, learn from their trainers’ experience, and gain technical support to help pass the final qualifying examinations.
NDT is set to become even more important in the future as the emphasis on safety and prevention of damage to the environment through loss of containment continues across all industries and within society as a whole. With new technological solutions and advances in techniques always coming to fruition, it is an exciting and interesting time to be an NDT technician.